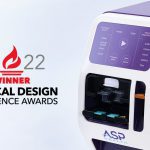
Single-Use Technologies, also known as disposables, play a crucial role in the success of cell and gene therapy manufacturing. Disposables come into contact with precious patient cells, making quality the top priority. Additionally, disposables contribute to the generation of recurring revenue for tools manufacturers, which is vital for market success. The ultimate objective is to optimize the cost-effectiveness and manufacturing ease of disposables to ensure consistency and high quality. In this article, we will delve into five key questions you should consider when developing single use disposables.
1. Are the disposable and instrument being developed together?
In cell therapy, instruments and disposables are like a lock and key. They need to fit together seamlessly and so should be developed together, ideally by the same company or two companies that are closely aligned and integrated. Developing them together is not only the most efficient process, it also generally leads to better quality products.
The first step in development is the product architecture. If the instrument or disposable is developed in isolation there is a risk of making both more complex and hence more costly than they need to be. There is always a trade-off between where most of the complexity, and thus cost, lives (instrument or disposable). Once the cost is designed into a disposable it is very difficult to remove, so careful consideration early in development can determine long term success. Developing the instrument and disposable together allows you to make trade-off decisions between cost (of both the development and the end product) and architecture complexity, to optimize efficiency and reach the best commercial outcome.
In addition, developing the instrument and disposables together can also improve system performance, primarily as the core functionality can be tested to identify issues such as any impact on loss of cells or cell viability. You can then take steps to minimize these issues – leading to a more reliable and higher quality product.
2. Is your disposable easy to use?
When speaking to cell and gene therapy developers who are evaluating tools, usability is often called out as a key consideration for adoption. This includes both the physical handling of the disposable and the instrument, as well as the user interface. Key considerations for the disposable design are around ease of loading into the instrument, fluidic connectivity including input materials such as media, wash buffers etc., and integration with other unit processing steps.
As we scale up as an industry, there will be a shift from more manual processes conducted by experienced scientists and process engineers, to more automated processes run by technicians. Ease of use will then be even more important for throughput and safe and correct use. When you’re dealing with cells from very ill patients, you can’t afford processing failures.
If you don’t have usability expertise in your own team, make sure you choose a design partner with usability and human factors engineering skills. They will bring the expertise to design out potential risks in your disposable, so you can minimize the risk of user error.
3. How will your disposable integrate with other systems?
It is well known that advanced therapy manufacturing workflows are complex processes with multiple unit processing steps. Even if your product focuses on a specific step within the process workflow, it is essential to have a comprehensive understanding of the upstream and downstream steps. This knowledge will greatly impact the format and design choices for your disposable.
At the early stages of clinical scale, it is important to have flexible input options for cell transfer, allowing users to connect their own input and output containers. However, as the industry expands and interfaces with different systems, it becomes necessary for disposable components to accommodate these variations. For instance, sterile connections of tubes can be achieved through tube welding in the early clinical stages, but as the user base grows, challenges arise when connecting tubes of different materials (PVC, C-Flex® etc.) and sizes. Sterile connectors provide a safe and convenient solution, but can be costly, so the potential benefits must be carefully evaluated. In an ideal scenario, standardization of tubing and connectors would be implemented. This may become a reality as the industry continues to grow and volumes increase, but currently it is not available.
So what can you do?
As a creator, we suggest gathering information and partnering with experienced designers to think through the critical success factors in your disposable and integration with other systems. It’s so important to get this right, as it greatly impacts user adoption. Complexity of integration may cause potential clients to move onto a perceived less complicated solution. There is no silver bullet, but with careful consideration, you can come up with a solution that gives you the best chance of commercial success.
4. What is your disposable manufacturing process – how do you ensure quality?
In GMP manufacturing, quality is king as the disposable will come into contact with patient cells. There are also regulatory requirements that need to be met for human clinical trials. It’s therefore a good idea to be considering manufacturability from the early phases of development.
The disposable is a critical component of the therapy manufacturing process, so every aspect of your disposable production will be assessed by drug developers. Users will examine the disposable itself and analyze each step of the supply chain to ensure quality standards and traceability can be maintained. Therefore, it is essential that you have control of your disposable supply chain, and for extra insurance against unexpected events, ideally have second source supply options for critical components.
Development firms with manufacturing expertise can help define the design specifications and manufacturing requirements to maintain quality and deliver on the commercial value proposition. They can help reduce production risk using best practice DfX (Design for Excellence) principles to create alignment around a production strategy to avoid problems at later stages.
5. What is your pricing strategy?
Disposable pricing is a key factor in commercial success. Users are price sensitive, while tools manufacturers count on disposables and reagents to create recurring revenue. You need to strike a balance between a price that your customers are willing to pay, while ensuring profitability.
This is particularly important for cell and gene therapy tools. While many products in industries like diagnostics can expect to see their transfer price reduce as volumes grow, this is not always the case for cell and gene therapy tools. Due to the new and personalized nature of the industry, volumes tend to stay relatively low and steady until a therapy is approved, and even then growth has been slow to date. This means you are unlikely to see the same volume growth in manufacturing and subsequent cost reduction and increased margins as would be expected for diagnostic disposables. Therefore, we suggest that margins needed for company sustainment are built in from the start. It is a difficult but crucial step to price the disposable low enough to attract new customers, while maintaining high quality and building in profitability.
Summary
When creating a cell and gene therapy tool, your disposable is just as important as the instrument as it is the critical cell contact element. To ensure the highest adoption and usage, instruments and disposables should be considered as a system and designed holistically to maximize efficiency and ease of use. When developing your disposable, it is best to consider early how it: fits into the workflow, interfaces with the instrument, can be safely manufactured to the highest quality standards, and how to strike the balance between affordability and profitability.
Want to learn more? Meet Brian Hanrahan at Phacilitate’s Advanced Therapies Week in Miami, January 16-22 or get in touch.